
They also allow you to export edited models as STL files ready to process via a slicer program ready to send to a 3D printer. The extensive model editing tools are also available to modify an STL file as you would any other CAD model type.įor example, you can add shapes, remove sections, and slice and cut planes much more effectively, granting you the same creative freedom as other file formats. Many feature STL repair functions, which are essentially automatic wizards that take the heavy lifting out of detecting and fixing minor errors, generally holes, shell discrepancies, intersecting triangles, and re-meshing for STL file optimization.
AMAZING SKETCHUP MODELS SOFTWARE
CAD or Computer-Aided Design softwareĪlthough not natively intended for STL file editing, CAD software is more than fit for editing and repairing STL files. Export the edited and repaired STL file.
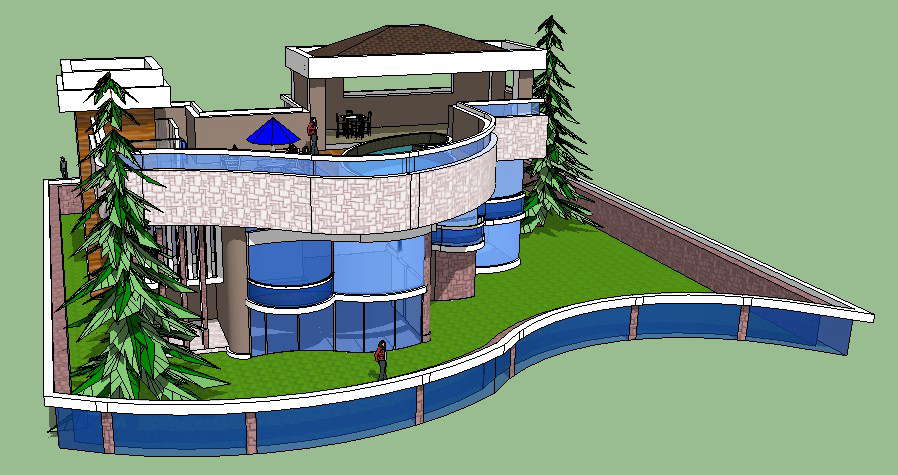
There are generally four steps involved, which can differ in complexity and process depending on the editor: To edit an STL file, you’ll first need an STL file editor. Though the STL file format is most commonly used to store the raw triangular mesh data for designs destined for 3D printing, other popular applications include rapid prototyping and computer-aided manufacturing. The main reason being STL files don’t generally exceed a few MB in file size, making them quick and easy to download. It’s also the file format of choice among hobbyists and makers for disseminating finished models, objects, and parts on community-sharing websites such as Thingiverse and MyMiniFactory. All slicers work with STL files – they’re the main file format of choice for 3D printing. One of the main benefits of the STL file format is widespread adoption by 3D printing slicer software. The process can degrade the overall resolution of the model and lower fidelity as the tessellation is more an approximation than a replica.īut, these discrepancies are generally negligible or easily fixed for the purposes of 3D printing.
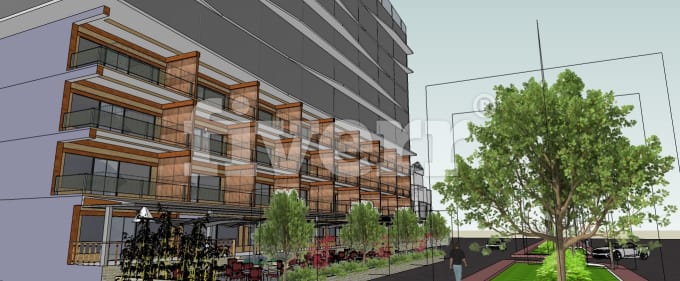
The resulting file doesn’t describe texture, color, scale, or units.ĭoing so effectively transforms the model into a collection of tiny triangles that drop in size but grow in number as a model’s complexity increases but remain vastly simpler than traditional CAD-generated surfaces and, especially, curves. Unlike other CAD file formats, which feature a host of information about a specific 3D model’s complex surfacing and geometry based on curves and splines (OBJ being one popular example), STL converts surfaces to a mesh or cloud of triangular faces and vertices through a technique known as tessellation.
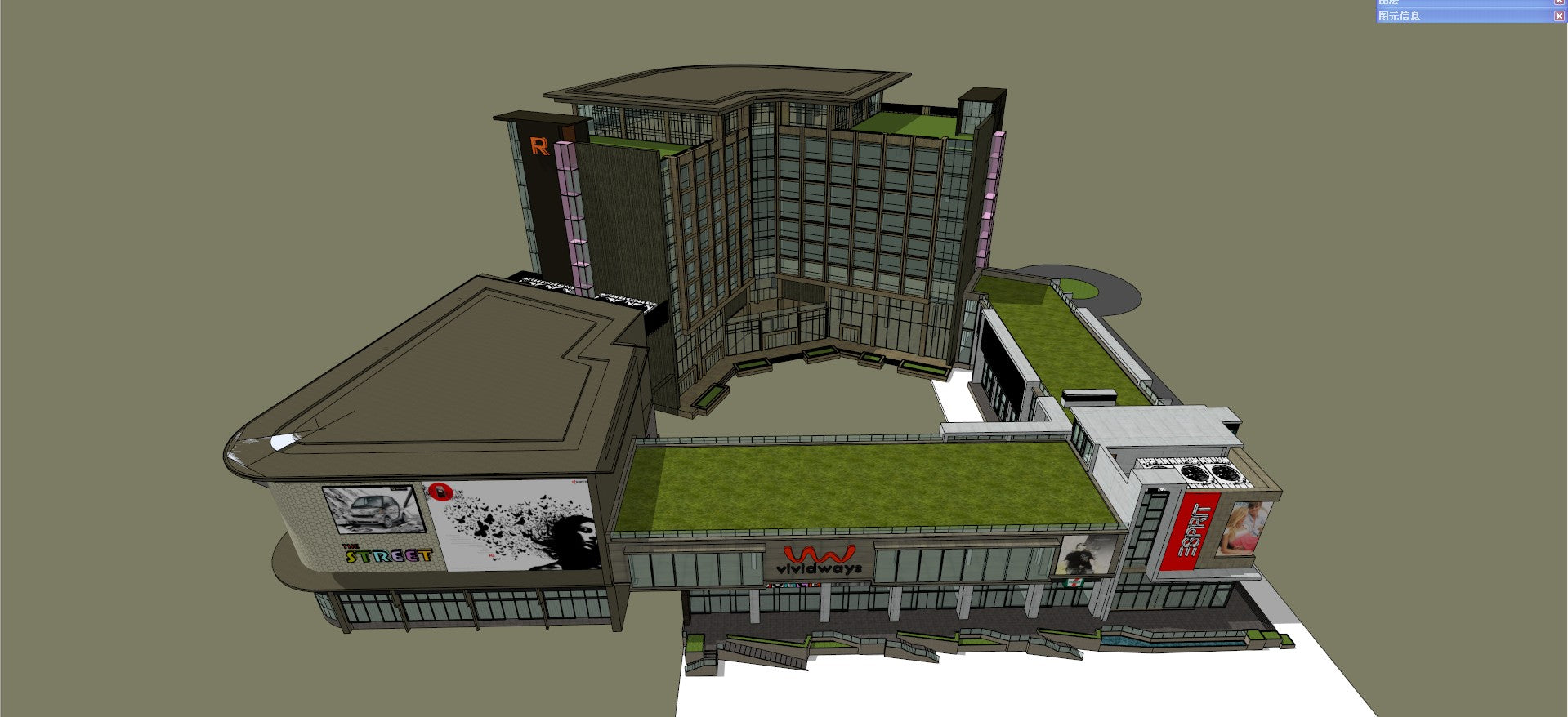
The idea was to create a file format as a simple and lightweight vessel for a 3D CAD model that’s easy to output to a 3D printer.
